After thorough consideration of proposals received in the Fall 2024 Seed Grant RFP, IConS chose two projects that align best with its mission to advance innovation in sensors and sensor systems, while providing unique interdisciplinary training for graduate student teams.
The first project’s awardee PIs Januka Budhathoki-Uprety (Wilson College of Textiles, Department of Textile Engineering, Chemistry and Science) and Henry Oliver Tenadooah Ware (College of Engineering, Department of Mechanical and Aerospace Engineering) collaborated on their proposal.
Their project, Developing High-Throughput 3D Printed Precision Macro-Sensors Using Engineered Nanosensors, aims to create next-generation optical biosensors by combining advanced materials and cutting-edge technology.
Budhathoki-Uprety expressed excitement about the project’s potential: “This is an exciting opportunity. The ability to produce high-resolution precision geometry optical sensor objects will open unprecedented opportunities in many fields for wireless monitoring of signals. Some examples include precision biosensors that could be implanted within complex biological spaces, integrated into specialty/technical textiles for healthcare and environmental monitoring, or aerospace engineering and structural health monitoring.”
Ware, from the Digital Light Manufacturing and Polymeric Materials (DLMPM) Lab added, “We within the DLMPM Lab are very excited by this opportunity. We aim to show that this rapid fabrication technique can be extended to smaller geometries and softer materials, such as hydrogels. We believe the interplay between materials and the manufacturing process will help to yield these next-generation sensors.”
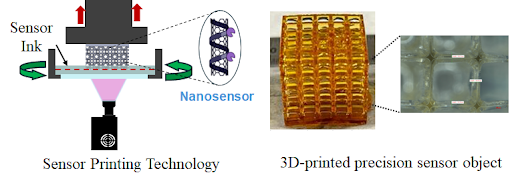
Precise and accurate sensors are essential for diagnosing complex problems in biological and man-made systems. Researchers must focus on both materials and manufacturing methods to develop these sensors. Single-walled carbon nanotubes (SWCNTs) that exhibit non-photo bleaching fluorescence in the near-infrared spectrum are promising materials for optical sensor material. Sensors can be designed to respond specifically to certain molecules and environmental conditions by tuning their surface properties.
While 3D printing has mainly been used for creating prototypes, a newer method called continuous liquid interface production (CLIP) has made it possible to mass-produce complex shapes that traditional manufacturing methods cannot achieve. CLIP can print intricate objects within minutes, depending on the printing conditions, material properties, and the height of the part. Items such as high-performance shoe midsoles and advanced athletic helmet padding are examples of what CLIP technology can produce. However, this technology is still young, and there’s a need to expand the range of materials it can work with.
In this research project, Budhathoki-Uprety’s lab will contribute expertise in developing SWCNT-based optical sensors, while Ware’s lab will focus on creating 3D printable inks and using microscale-focused CLIP (microCLIP) technology to produce the 3D sensing platforms. By combining these technologies, the resulting sensors could improve personal health management, make disease diagnosis more accurate, enhance treatment strategies, and accelerate drug discovery.
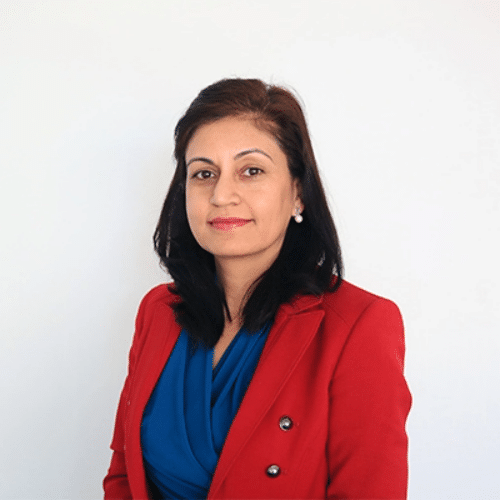
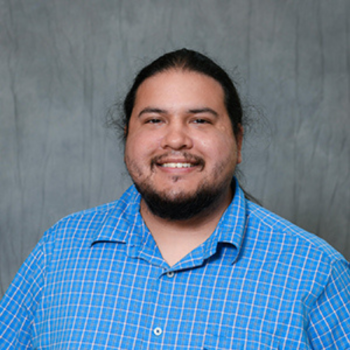